EBNER | Customer Services
CUSTOMER SERVICES.
Global Service. Unmatched Expertise.
The EBNER global service network provides expert support for all heat treatment plant challenges, leveraging our extensive experience and innovative analysis methods. EBNER´s comprehensive service portfolio includes:
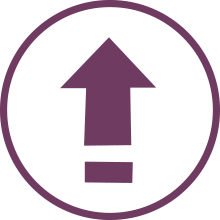
UPGRADE & REBUILDS
UPGRADE & REBUILDS
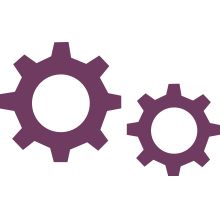
SPARE PARTS
SPARE PARTS
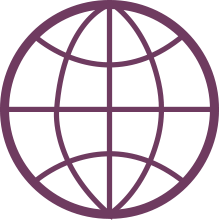
GLOBAL SERVICES
GLOBAL SERVICES
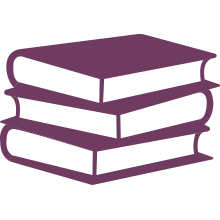
TRAINING & WEBINARS
TRAINING & WEBINARS
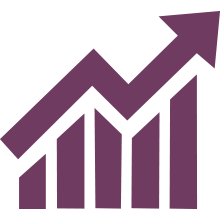
PROCESS DEVELOPMENT
PROCESS DEVELOPMENT
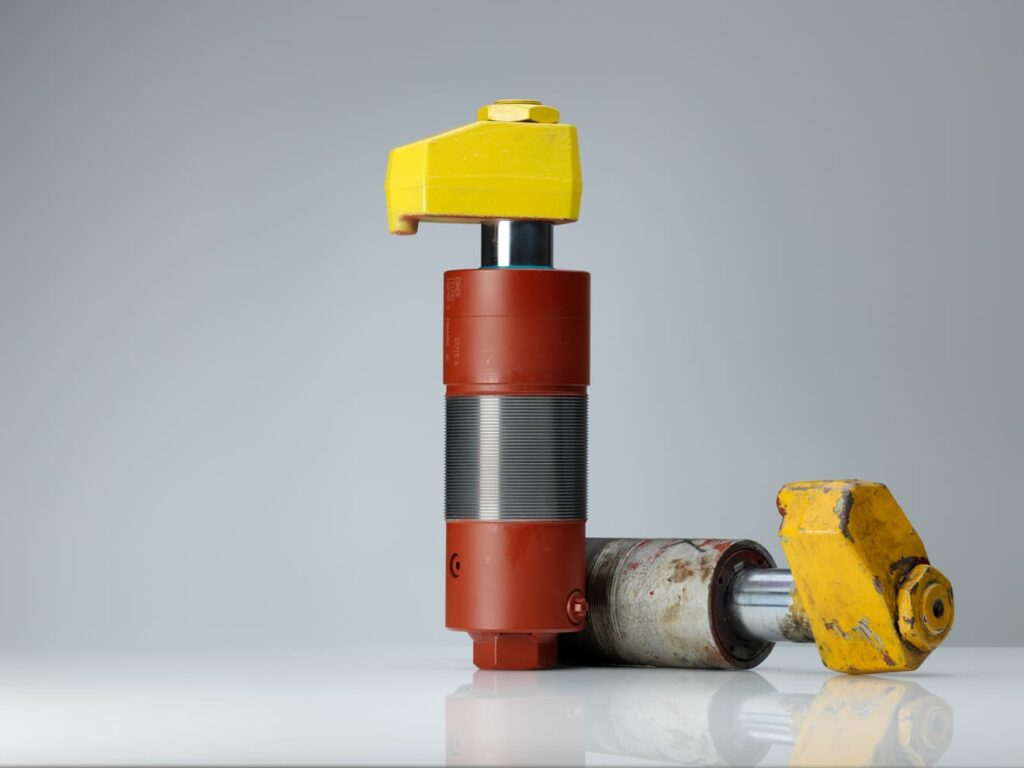
SPARE PART SERVICE.
Spare part availability is an important element in ensuring efficient, safe production. On the other hand, the individual requirements of a facility’s owner are also critical in a modern industrial environment.
A team experienced in cooperating directly with our partners throughout the EBNER world, as well as efficient and rapid processes, ensures that top-quality spare and replacement parts are delivered when needed.
Our product portfolio ranges from simple relays to complex component assembly groups, on up to individually-fabricated inner covers.
SIMULATION AS A SERVICE.
In our in-house lab in Leonding, Austria you can use our SIMCAL facility for your trial anneals. Our experienced staff is available to assist you. They will carry out the trials for you, and on request can also analyze the samples after testing has been completed.
Our lab is equipped with a wide variety of equipment for analysis and evaluation, including a tensile testing machine, hardness testers, microscopes and sample preparation equipment, equipment to conduct chemical analyses and an Epstein testing device to analyze magnetic properties.
We would be happy to advise you on the services we offer and help you develop a testing plan.
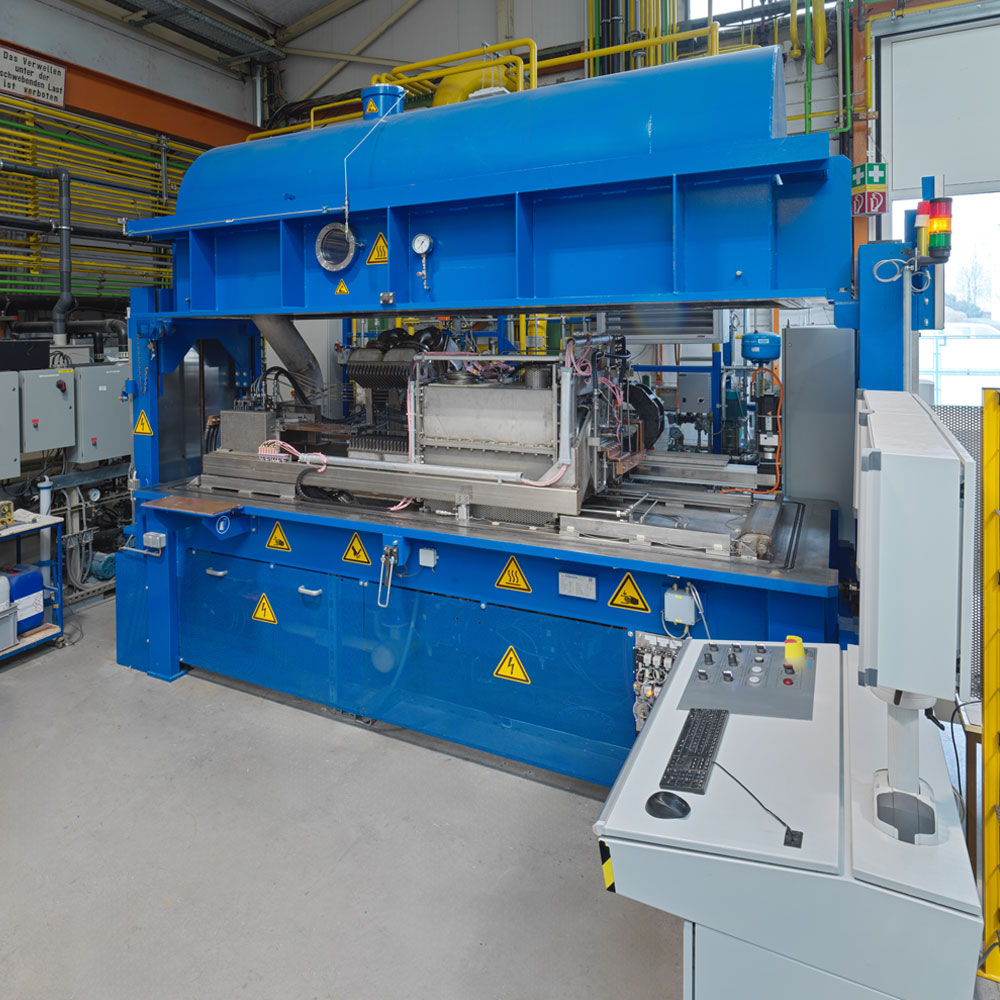
Global Service.
Unmatched Expertise.
At EBNER, we offer a full suite of services. Our goal is to ensure the highest standards of safety, efficiency, and sustainability, providing our customers with cutting-edge solutions that enhance performance, reduce operating costs, and secure a competitive edge in a rapidly evolving industry.
Relocating and recommissioning heat treatment systems requires a comprehensive inventory,
careful disassembly, secure transport, precise assembly, and thorough recommissioning. A detailed risk assessment and process optimization are essential to ensure safety, maximize efficiency, and ensure smooth operation at the new location. Proper assembly and recommissioning are prerequisites for high-quality production and minimized production downtime.
Process optimization of a heat treatment system aims to shorten cycle times, improve quality,
reduce gas consumption, and enhance performance. Targeted measures lower operating costs
and accelerate production. This increases the overall efficiency of the system and strengthens
the competitiveness of our customers, ensuring more sustainable and profitable production.
Precise selection is crucial for modernizing and procuring spare parts for heat treatment systems from EBNER and other manufacturers. The use of compatible components and innovative technologies are prerequisites for the reliability and optimal performance of a heat treatment system, while minimizing operating costs and maximizing productivity.
A modernization offers you the opportunity to do the following:
- Integrate new technologies
- Upgrade control systems
- Improve energy efficiency
- Adapt existing equipment to meet changing safety standards
Our service for heat treatment systems encompasses everything from detailed inventories and
safety device inspections to precise gas heating adjustments and thorough annual maintenance. EBNER service personnel offer comprehensive care that optimizes performance and ensures the safety and lifespan of the heat treatment system.
Metallurgical and technological simulations (CFD/FEM) optimize furnace design, predict heat transfer, and ensure uniform temperature distribution. This translates to reduced energy consumption, improved product quality, and extended furnace life. Precise material analyses help to determine the optimal heat treatment parameters for the specific materials. This includes measuring key mechanical properties like hardness, strength, and ductility, along with microstructural features.
Transform your heat treatment facilities with our advanced upgrades for decarbonization. With state-of-the-art innovative heating systems such as H2 hydrogen burners, electric heating technologies and the use of alternative fuels, a significant reduction of CO2 emissions and an increase
energy efficiency at the same time. EBNER‘s reliable and sustainable technologies remain competitive advantage in an environmentally conscious future.
Our In-House/On-Site training program for heat treatment systems covers training and knowledge transfer for maintenance personnel, system operators, measurement and control technicians. These specialized trainings are designed to strengthen expertise and maximize operational efficiency, ensuring safe and effective system performance.
CUSTOMER SERVICES NEWS.
News 2025-06-10
Save maintenance and hardware costs!
Replace your Hydraulic Numeric Controller (HNC) unit with an EBNER software solution! Our software solution, referred to as “pusher mechanism synchronization control”, was developed by EBNER and has already been successfully implemented at several customers’ facilities. Due to the fact that HNC devices will no longer be manufactured in their original forms, this is the perfect time to step up to this state-of-the-art solution and EBNER technology.
News 2025-01-22
Saving electricity costs and CO2?
With Cyplan® ORC technology from our industrial partner Dürr, you have the opportunity to convert the waste heat from your EBNER vertical strand annealer into electricity and thus significantly reduce your energy expenses!
News 2024-05-19
Reduce operating expenses with our H2 regeneration system for bright annealing lines
If your bright annealing line has been hit hard by the high price of hydrogen, we have the solution for you:
a fully integrated EBNER H2 regeneration system!
News 2023-12-14
10% discount* on the latest generation of control plug couplings for EBNER bell annealers
The plug inserts and housings for automatic bell annealer electrical couplings are unfortunately no longer available from the manufacturer. Here at EBNER, we would like to continue to offer the best service available and prevent long waiting times for spare parts – which is why we would like to assist you in upgrading to the latest generation of components.
News 2023-10-13
SERVICE your facility NOW AND SAVE!
You want your facility to function as trouble-free and efficiently as it can?
You want to be kept up to date on the latest technological developments?
AND you want to save money?
News 2023-04-18
Save more than € 100,000 / year!
As the user of a bell annealer facility, you too are faced with the issue of rising operating costs. A chart of the current trends in energy prices shows that the price for electricity rose dramatically during the last years, and a similar problem can be seen with hydrogen – the demand for hydrogen rose dramatically, as did its price. Combined with the relatively high costs of producing hydrogen, predictions agree that prices will remain high over the next few years.
TECHNICAL SUPPORT. AROUND THE GLOBE. CLOSE TO YOU.
EBNER Industrieofenbau
Ebner-Platz 1
4060 Leonding / Austria
Service hotline:
Monday – Thursday 7:00 a.m. – 4:30 p.m. | Friday 7:00 a.m. – 1:00 p.m.
Phone: (+43) 732/68 68 8200
After hours: (+43) 732/68 68
Fax: (+43) 732/68 68-68299
E-Mail: [email protected]
EBNER Furnaces, Inc.
224 Quadral Drive
Wadsworth / Ohio 44281 | USA
Service hotline:
Monday – Friday 7:00 a.m. – 4:00 p.m.
Phone: (+1) 330/335-1800
After hours: Emergency Pager Service
Fax: (+1) 330/335-1605
E-Mail: [email protected]
EBNER Industrial Furnaces
Beijing East Road 82
215400 Taicang / Jiangsu | China
Service hotline:
Phone: (+86) 512 5357 6868
Fax: (+86) 512 5357 6867
E-Mail: [email protected]
EBNER India Pvt. Ltd.
L&T Seawoods, Unit No.: C-402 | 4th Level | C wing | Tower 1 | Plot R-1 Sector 40
Seawoods Railway Station | Nerul Node | Navi Mumbai – 400706 | INDIA
Service hotline:
Phone: (+91)22 6139 3333
Fax: (+91)22 6139 3311
E-Mail: [email protected]
EBNER Japan – K. Brasch & Co., Ltd.
Y’s Bldg. Room 402
2-13, Tsukishima 1-chome
Chuo-ku, Tokyo 104-0052
Service hotline:
Phone: 03/5560 7591
Fax: 03/5560 7595
E-Mail: [email protected]
CUSTOMER SERVICES.
Across the globe, we can offer you on-site support, maintenance and spare part sales.
Simply contact our Customer Services department.
To ensure that the availability and cost effectiveness of your EBNER facility remain as high as possible, we recommend having your facility inspected and maintained at regular intervals. Contact us now to schedule a time to consult our experts.
REPORTING MALFUNCTIONS.
Service hotline:
Monday to Thursday 7:00 a.m. – 4:30 p.m.
Friday 7:00 a.m. – 1:00 p.m
(+43) 732/68 68 8200
After hours:
(+43) 732/68 68