EBNER | Products | Strip cleaning facility
Strip cleaning systems.
for integration into continuous strip processing lines or as stand-alone line
Following a cold rolling process, the surface of metal strip is contaminated with rolling oil, emulsion, and iron fines. To ensure that any subsequent heat treatment process provides a clean strip surface, oil and iron residues must be removed before heat treatment begins.
Excessive amounts of oil residue and iron fines can affect the dewpoint of the furnace atmosphere, which may in turn limit the quality of the strip surface.
EBNER strip cleaning lines are distinguished by the high quality of their manufacture and their excellent cleaning performance, which they combine with an extremely low consumption of demin water and cleaning chemicals.
Advantages of the EBNER design:
Demin water in zone 1 / high-pressure zone
Oil and water are efficiently separated using a full-flow filtering system, which employs a band screen filter and a coalescence filter.
- The system facilitates oil disposal, as it can simply be placed in a waste oil tank
- Water, once free of oil, is reused
- This reduces the consumption of fresh water
- This reduces the consumption of lye by around 50 % in comparison to a standard strip cleaning system design
- Automatic conductivity measurement to regulate lye concentration
- Automatic admixture of lye and fresh water
- Automatic adjustment of brush rolls when brush bristles are abraded or worn
- Automatic conductivity measurement of rinsing water
- Automatic admixture of fresh water
- Each cascade is equipped with its own recirculation system
- The use of cascades and the recirculation/reuse of rinsing water mean that only a small amount of fresh water is consumed
- The effectiveness of the last squeeze roll unit is ensured through the use of fleece rolls
Zones are separated by squeeze rolls units to prevent the mixing of liquids between zones
Upper squeeze rolls are precisely guided during vertical upward-downward travel
- This precision ensures that the axes of the upper and lower squeeze rolls are exactly parallel with one another
- The parallel alignment prevents the strip from off-tracking to the side
- Correct tracking prevents the creation of wrinkling, particularly with very thin (< 0.2 mm) production strip
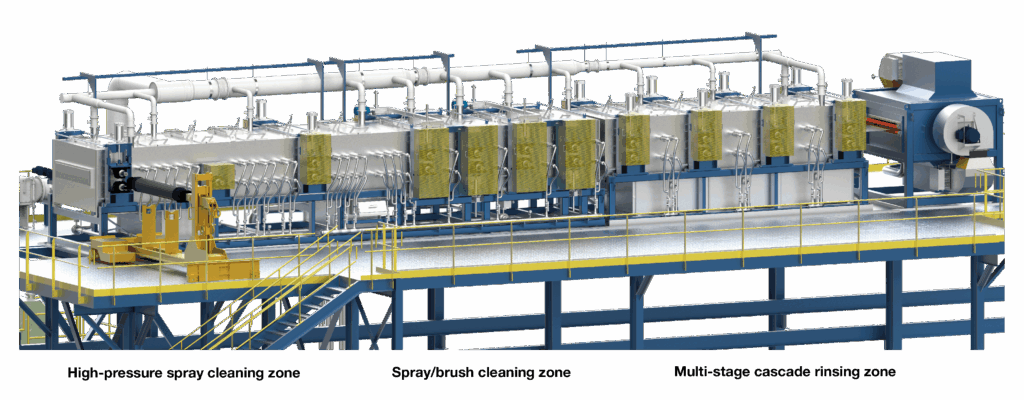
Structure of the Strip Cleaning Facility:
An EBNER strip cleaning line is generally divided into
three main zones.
- High-pressure spray cleaning zone
- Spray/brush cleaning zone
- Multi-stage cascade rinsing zone
A HICON® dryer is positioned downstream of the third
zone.
- Hot air is blown onto the strip through an array of slot nozzles by two recirculation fans.
- Any residual moisture on the strip surface is fully removed.
The lengths of the individual zones, as well as the total overall length, depend on the time the strip requires in each zone and thus on the maximum speed of the strip as it travels through the strip cleaning line.
Heating modes for the cleaning agents:
EBNER offers the following types of systems for heating the cleaning agents (demin water and lye) and dryer:
- Electric heating system
- Natural gas heating system
- Steam heating system
In addition to these options, EBNER offers systems to recycle the thermal energy of the furnace exhaust gas, employing it to heat the dryer or as a supplementary heating method for the cleaning liquids.
Such systems allow energy costs to be significantly reduced.
Features of the EBNER strip cleaning system
- Circulation pumps, supported by stand-by pumps on request
- Special equipment, such as magnetic filter systems
- Sensor systems:
- Level measurement
- Flowrate measurement
- Pressure measurement
- Temperature measurement
- Conductivity measurement
- Tanks are insulated to prevent radiant heat losses
- Extracting steam from all zones of the in-line tank
- The drives of the squeeze and brush rolls employ frequency-controlled motors and universal cardan shafts
- Roll changing device
- Demin water preparation station can be supplied as an optional extra or by the purchaser
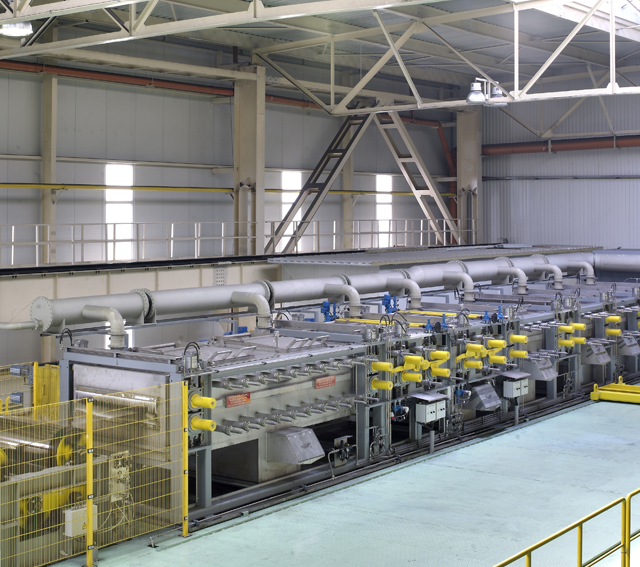
Applications.
Steel industry.
- Austenitic CrNi alloy steels
- Ferritic Cr alloy steels
- Martensitic Cr alloy steels
- FeNi alloys
- Ti alloyed steels
- Mn alloyed steels
- Co alloyed steels
- Clad steel strip
- Duplex steels
- Titanium and Ti alloyed steels
- AlCr alloyed steels
Copper base metals industry.
- Copper and copper alloys
- Phosphor bronze
- Nickel silver
- Special alloys