EBNER | Products | HICON/H2 SIMCAL Annealing simulator for continuous heat treatment facilities
Annealing simulator for continuous heat treatment facilities
HICON/H2 SIMCAL as a Complete Facility or a Service
- Flexible
- Quick Realization
- Efficient
Continuous heat treatment facilities are complex systems, with many parameters that can influence a process (heating-up rate, cooling rate, atmosphere composition, dewpoint, strip tension, etc.) and provide a product with particular properties (specific mechanical and magnetic properties, microstructures, phase transformations, etc.).
Efficient manufacturing, optimized processes and the development of new products are critical factors for modern companies as they seek to remain competitive.
When continuous heat treatment facilities are involved, these factors become even more difficult to assess: the facilities, which are typically extremely large, either have to halt production or do not have the flexibility to reliably follow a desired testing program.
For these reasons, simulating heat treatment processes at laboratory scales is far more efficient and much quicker to organize.
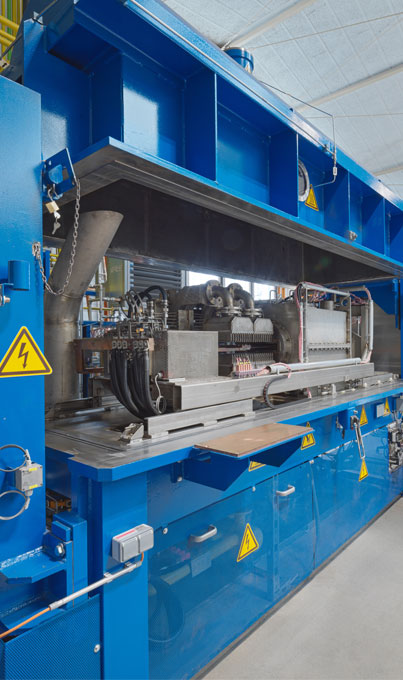
Realistic simulation of annealing processes due to EBNER know-how
When simulating continuous heat treatment processes, the challenge is to recreate the processing conditions within the real facility as accurately as possible.
- The first step is to use strip with an identical thick-ness. With thick strip this is relatively simple, but the problem becomes increasingly complex as the strip becomes thinner.
- The process atmosphere (composition, dew point) must also be a match with that in the real facility. This may mean that some safety-related challenges may have to be met (e.g. when using H2 as an atmosphere).
- The temperature profile (heating and cooling curves) must correlate with the real ones, as does the temperature uniformity that is achieved.
- In some processes, strip tension can have a significant influence on results. In a simulation, the tension must therefore either match the actual conditions or be dynamically adjusted to match the fictitious travel path of the strip.
In a simulation, comparable material properties can only be achieved if all of these factors are taken into account.
HICON/H2 SIMCAL Keyfacts
For this application, EBNER has developed an extremely flexible, gas-tight annealing simulator with the following specifications:
- Strip thickness: 0,2 – 3,0 mm
- Length of sample: 300 – 500 mm
- Width of sample: 30 – 200 mm
- Temperature: bis zu 1.260 °C
- Process atmosphere: 100 % H2 bis 100 % N2, H2/N2 Mischungen, Argon, Helium
- Dewpoints: + 20 °C bis – 55 °C
- Dynamic strip tension adjustment during the entire heat treatment cycle (a perfect representation of a vertical furnace is thus also possible)
- Fast cooling: bis 200 k/s.mm
- Slow cooling: 5 – 25 K/s
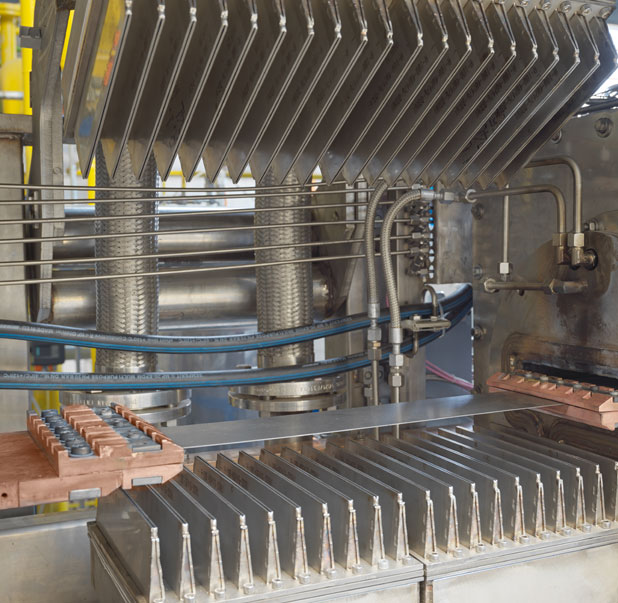
Advantages of an annealing simulation
- The opportunity to analyze and improve the understanding of existing processes
- Decisions that affect the process can be made more quickly and accurately
- Heat treatment processes and material properties can be optimized
- New material grades can be developed and made market-ready more quickly
- Annealing cycles can be developed that achieve particular target qualities with different starting materials (e.g. varying chemical compositions / upstream processing steps)
- Improvement of throughputs through a better understanding of material-specific process windows and more efficient transitions when strip parameters or formats change
- No need for expensive and labor-intensive “full-scale” trials at production facilities
- Improve the productivity and profitability of facilities